Review Article, J Soil Sci Plant Health Vol: 6 Issue: 1
Development of Geopolymer Concrete based on Reactivity of Fly Ashes: A Review
Bishal Bhusal*, Rajan Suwal, Kamal Bahadur Thapa
Department of Agriculuture, Tribhuwan University, Kirtipur, Nepal
*Corresponding Author: Bishal Bhusal
Department of Agriculuture,Tribhuwan University,Kirtipur,Nepal
E-mail:bhusalroshan10@gmail.com
Received date: 01 December, 2021, Manuscript No. JSPH-21-35187;
Editor assigned date: 03 December, 2021, PreQC No. JSPH-21-35187 (PQ);
Reviewed date: 15 December, 2021, QC No JSPH-21-35187;
Revised date: 21 December, 2021, Manuscript No. JSPH-21-35187 (R);
Published date: 03 January, 2022, DOI:10.4172/jsph.1000123
Citation: Bhusal B (2022) Development of Geopolymer Concrete based on Reactivity of Fly Ashes – A Review. J Soil Sci Plant Health 6:1.
Abstract
Concrete is the world’s most useful, durable and reliable construction material. Next to water, concrete is the most used material in the world. Ordinary Portland cement production is the second only to the vehicles as major source for generation of carbon dioxide (CO2) gas, which not only pollutes the atmosphere but gradually increases the temperature of Earth. The emission of carbon dioxide (CO2) gas and energy requirement in the production of Ordinary Portland Cement (OPC) causes the continuous depletion of ozone layer and global warming problem. Additional huge amount of energy is also consumed for production of the cement. So, it is necessary to find out an alternative material source since limestone is the major source for the production of Portland cement there may be acute shortage of limestone in next 25 to 50 years. The introduction of Geopolymer concrete (GPC) technology in the construction industry leads to sustainable development and cleaner environment by reducing environmental pollution. Geopolymer concrete is an innovative construction material which shall be produced by the natural process of inorganic molecules and have advantageous benefit of longer service life, low carbon emission, recycled industrial waste, durable properties, and high strength.
Keywords: Geopolymer concrete; Fly ash; Alkaline solution
Introduction
In 1978, a French professor named Davidovits coined the term geopolymer to describe a wide spectrum of materials characterized by networks of inorganic molecules. The Geopolymers rely on thermally activated natural materials like Meta kaolinite or industrial by products like coal based fly ash or slag to provide a source of silicon (Si) and aluminum (Al). These Silicon and Aluminium is dissolved in an alkaline activating solution to become the binder.
“The polymerization process involves a fairly quick chemical reaction process under alkaline conditions on silicon aluminum minerals that ends up in a three-dimensional polymeric chain and ring structure,”.
In the case of geopolymers prepared from fly ash, the role of calcium in these systems is incredibly important, because its presence can result in flash setting and thus must be carefully controlled [1]. The source material is mixed with an activating solution that provides the alkalinity needed to liberate the Si and Al and possibly with an additional source of silica.
Literature Review
The temperature during curing is incredibly important, and depending upon the source materials and activating solution, heat often must be applied to facilitate polymerization, although some systems are developed that are designed to be cured at room temperature exceptional qualities of Geopolymer concrete are set at room temperature.
•Nontoxic, bleed free
•Long working life before stiffening
•Impermeable
•Higher resistance to heat and resist all inorganic solvents
•Higher compressive strength
Compressive strength of Geopolymer concrete is higher compared to the ordinary Portland cement concrete. Geopolymer concrete also showed very high early strength. The compressive strength of Geopolymer concrete is about 1.5 times higher than that of the compressive strength with the ordinary Portland cement concrete, for the same mix.
Background
French researchers used the term "geopolymer" in the 1970s to describe a class of source materials created by reacting an alkaline solution with an aluminosilicate powder.
The need for concrete is steadily rising to meet the growing demand for infrastructure development. It is common knowledge that the manufacture of OPC requires a huge amount of natural resources and energy, as well as emits a significant amount of carbon dioxide into the atmosphere. Therefore, it is essential to find alternatives to make the concrete environment friendly. The emission of CO2 and energy requirement in the production of Ordinary Portland Cement (OPC) causes the continuous depletion of ozone layer and global warming problems. The introduction of Geopolymer Concrete (GPC) technology in the construction industry leads to sustainable development and cleaner environment by reducing environmental pollution.
According to the recent research, it was reported that CO2 reached to its highest record of 417.1 ppm and year’s 2018 value is 2.4 ppm higher than last year value. This value creates an alarming situation as increase in CO2 level impacts the environmental conditions like an increment in atmospheric temperature and pressure. This increment can affect the CO2 adsorption on amorphous silica surfaces and can change the amorphous nature of materials to crystallization phases. That is why the production of cement is considered unsustainable due to the high emission of greenhouse gases.
Fly ash is also known as pozzolanic material because it contains silica and alumina, which have little or no cementitious value on their own but will chemically react with calcium hydroxide at ordinary temperatures (in finely divided form and in the presence of moisture)
to form compounds possessing cementitious properties, as defined by American concrete Institute. ASTM C618 is one of the most used benchmarks for fly ash characterization and classification, which divided fly ash into 2 classes, i.e. Class F is created by burning anthracite or bituminous coal, while class C is created by burning lignite or sub-bituminous coal.
Investigations on Geo Polymer Concrete (GPC) have revealed that it has equal or superior properties than Ordinary Portland Cement (OPC) Concrete. GPC can achieve strength comparable to OPC concrete in normal strength grade as well as GPC is a good fire resistant material, and it has a better performance in resisting sulphate attack and chloride. GPC is gaining acceptance due to its numerous benefits such as sustainable construction, longer service life, low carbon emission, recycled industrial waste, durable properties, and high strength.
Geopolymer binders have been shown to be environmentally friendly building materials capable of completely replacing OPC in the concrete industry. Geopolymer technology can utilise many by- product materials, such as Fly Ash (FA), Granulated Blast Furnace Slag (GBFS), palm oil fuel ash, rice husk ash, and mining wastes [2]. GPC can provide several environmental advantages also. The utilization of GPC can reduce CO2 emission up to 80% compared to OPC concrete by using industrial by-product waste materials such as Granulated Ground Blast Furnance Slag (GGBFS) and Fly Ash (FA) as a complete OPC replacement. It was also discovered that GGBS manufacture used less energy than OPC production in the same amount of time. Despite the fact that GPC is a very effective sustainable material, its use on buildings and other structural components is currently limited due to a lack of structural design standards and norms.
For GPC to be commercialized, more research into long-term behavior and durability is required. Geopolymer concrete is found to perform very well under the compressive strength tests. The tensile strength of GPC concrete is clearly superior to that of OPC concrete with the same compressive strength, according to the literature assessment. Sodium silicate solution is the main product of reaction resulting from the attack that combines with the gel produced by other particles during precipitation. The geopolymer paste which includes nano silica and nano aluminium oxide in it for high calcium based flyash yielded good strength and durability properties for particular molar concentration. GPC possess the ideal properties such as freeze- thaw resistance, lower shrinkage, corrosion and sulphate resistance. It remains sound without need of any repair. Geopolymer shows comparatively lesser strength loss and mass loss when compared to OPC and it yields high resistance to heat and acid attacks. The durability properties of geopolymer concretes enhances with time, filling the voids and cracks as it consists of the fine materials. The compressive strength of the geopolymer concrete is highly influenced by the amount of CaO content in the fly ash. Besides that, the compressive strength also increases as the amount of the hooked steel fibers increases.
The study of the literature reviews brings some specific areas which need to be addressed in order to overcome the limitations and make the geopolymer concrete a widely usable one. These areas are as follows, Curing methodology of the concrete, Molarity of the alkaline solutions, Uses of fly ash and other materials, Variation in incubation period and incorporation of cement as partial replacement. If only these areas are understood clearly then the geopolymer can come out as a noble and ecofriendly invention which can be used practically at
larger scale. That the fly ash is a sustainable material for future construction works. However design procedure must be created before geopolymer concrete can be used on the jobsite.
That the price of fly ash-based geopolymer concrete is estimated to be about 10 to 30 percent cheaper than that of Portland cement concrete. Assessed the performance of geopolymer concrete, both in material and structure. There are approximately six categories of geopolymer concrete based on alumina silicate sources, according to the findings. They are fly ash-based, metakaolin-based, slag-based, rice husk ash-based, high calcium wood ash-based and combination of either two of the earlier mentioned aluminosilicates. Among these types, fly ash-based geopolymer concrete is the most popular and widely tested also through review of papers found that geopolymer is suitable for structural elements. It was also found that the full scale tests are still lacking especially for non-Fly Ash based geopolymer concrete.
Proposed a method for selecting the mix proportions of fly ash based geopolymer concrete and their experimental results showed that the compressive strength of the fly ash based geopolymer concrete decreased linearly with increase in the water to geoploymer solids ratio. The optimum time of curing for fly-ash based geopolymer concrete is reported to be 20 hours to 24 hours. GPC has less water absorption, and less porosity as the geopolymer materials are finer than control concrete components. In the geopolymer mortars apparent porosity increases by adding silica fumes in flyash based geopolymer pastes.
In general, increase in the fineness of binder material increases the strength of Geopolymer. Out of all the available alkali activators, combination of Sodium silicate and Sodium hydroxide solution proved to produce fair activation of polymerization process. Also with the increase in the concentration of Sodium hydroxide there is an increase in the compressive strength.
From the reviews it is concluded that different sources (and even the same source, but different batch) of fly ash materials will give some different characteristics of the fly ash, where it would affect the synthesis process of the fly ash based geopolymer concretes. A good understanding of the influence of each characteristic of fly ash becomes essential because different properties of fly ash will lead to different properties of the geopolymer final products, to depart from that fact; it is not an exaggeration to say the fact. As a result, the remainder of this analysis will focus on the variations in fly ash properties and their impact on geopolymer synthesis, as well as the properties of geopolymer products [3]. Although there are so many researches that have been conducted, until now, there is still no clear and standardized guide about the making procedure of fly ash based geopolymer concrete, especially in terms of structural applications.
Fly Ash
Fly ash, the fine particulate waste material produced by pulverized coal-based thermal power station, it has a potential to be a resource material. As per IS 3812: 2003, the generic name of the waste product due to burning of coal or lignite in the boiler of a thermal power plant is pulverized fuel ash. Pulverized fuel ash can be fly ash, bottom ash, pond ash or mound ash. Fly ash is the pulverized fuel ash extracted from the fuel gases by any suitable process like cyclone separation or electrostatic precipitation. Pulverized fly ash collected from the bottom of boilers by any suitable process is termed as Bottom Ash [4].
ASTM C618 specified two categories of fly ash, Class C and Class F depending on the type of coal and the resultant chemical analysis. Class C fly ash, normally produced from the combustion of lignite or sub bituminous coals, contains CaO higher than 10 percent and possesses cementitious properties in addition to pozzolanic properties. Class F flies ash, normally produced from the combustion of bituminous or an anthracite coal contains CaO below 10 percent and possesses pozzolanic properties [5-7].
Classification, based on the boiler operations is classified with two distinct identities: Low Temperature (LT) fly ash, Generated out of combustion temperature below 900⁰ C: High Temperature (HT) fly ash, Generated out of combustion temperature below 1000⁰ C. This property together with a relatively low ignition loss makes HT fly ash more suitable for use in cement and concrete industries.
Sand
A fine aggregate which is either natural sand or crushed stone sand or crushed gravel sand. Natural Sand A fine aggregate produced by the natural disintegration of rock and which has been deposited by streams or glacial agencies. Crushed Stone Sand and Crushed Gravel Sand - A fine aggregate produced by crushing stone or natural gravel.
The sand shall consist of natural sand, crushed stone sand or crushed gravel sand or a combination of any of these. The sand shall be hard, durable, clean and free from adherent coatings and organic matter and shall not contain the amount of clay, silt and fine dust.
Deleterious material the sand shall not contain any harmful impurities such as iron pyrites, alkalis, salts, coal or other organic impurities, mica, shale or similar laminated materials, soft fragments, sea shells in such form or in such quantities as to affect adversely the hardening, strength or durability of the mortar.
Limits of deleterious material unless found satisfactory as a result of further tests as may be specified by the engineer-in-charge, or unless evidence of such performance is offered which is satisfactory to him, the maximum quantities of clay, fine silt, fine dust and organic impurities in the sand shall not exceed the following limits:
Sampling the method of sampling shall be in accordance with IS: 2430-1969. The amount of material required for each test shall be as specified in relevant parts of IS: 2386-1963.
Testing any test which the purchaser or his representative may require in connection with this standard shall be carried out in accordance with the relevant parts of IS: 2386-1963. Unless otherwise stated in the enquiry or order, duplicate tests shall be made to all cases and the results of both tests reported [8].
If further confirmation as to the satisfactory nature of the material is required, compressive test on cement mortar cubes (1: 6) may be made in accordance with IS: 2250-1981: using the supplied material in place of standard sand and the strength value so obtained shall be compared with that of another mortar made with a sand of acceptable and comparable quality.
Aggregate
Quality of aggregate is considerable important because it has three quarters of the volume of fly ashes based concrete. Quality of aggregate effects on strength of concrete, durability and structural performance of concrete. Aggregate consider as an inert material dispersed throughout the paste largely for economic reasons [9]. In fact, aggregate is not truly inert and its physical, thermal and chemical properties influence the performance of concrete. Aggregate is cheaper than cement and it is, therefore, economical to put into the mix as much of the former and as little of the latter as possible. But economy is not the only reason for using aggregate; it confers considerable technical advantages on concrete, which has a higher volume stability and better durability than hydrated cement paste alone.
Water
The concrete mix are design with water cement ratio 0.5, accordingly the water locally available was checked to use for construction purpose as per IS 456–2000 clause no. 5.4, which is clean and free from injurious amounts of oils, alkalis, salts, sugar, organic materials or other substances that may be deleterious to concrete or steel.
Alkalis
A substance that has a higher pH level than. It can also be interchangeably used with base. The term alkali is used to name the group 1 elements of the periodic.
Physical properties of alkalis
Alkalis have the following properties:
•Alkalis have bitter taste and a slippery soapy
•Alkaline solutions have pH values greater
•Alkaline solutions turn red litmus paper to
Chemical properties of alkalis
There are four common reactions of alkalis:
•Neutralisation reaction
•Reaction with ammonium salt
•Precipitation of metal hydroxides
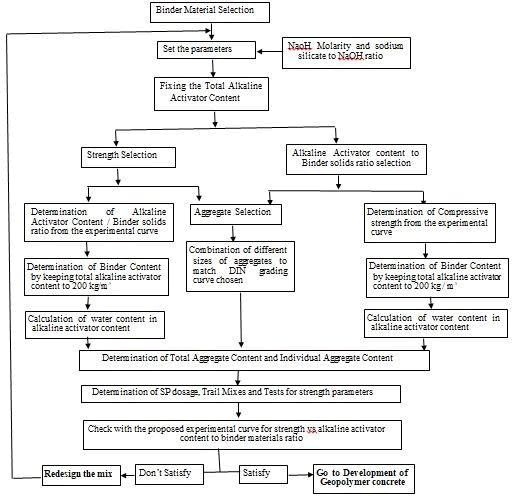
Figure 1. Flow chart representing mix design based on strength and activator to binder approach.
As per result drawn GGBS based Geopolymer concrete with fly ash gives excellent compressive strength values. That despite the huge researches that have been carried out, the geopolymer-based concrete faces many challenges that need to be addressed. One of the main challenges is the absence of the standards which should be created by a global committee. The creation of new codes will be very expensive so it requires the collaboration of governments, industries, and researchers. Regardless of the problems, the use of high calcium fly ash in geopolymer concretes can give higher compressive strength and also shows some strength development along with the age [10]. It can happen because then reaction involved is not only the polymerization but also the hydration reaction. However, this mechanism is still not clear and needs further research.
Reveals that further research and development of chemical admixtures which can be applicable in geopolymer concrete is needed. Revealed that Geopolymer concrete is gaining acceptance due to its numerous benefits such as sustainable construction, longer service life, low carbon emission, recycled industrial waste, durable properties, and high strength.
Conclusion
Concluded that the Geopolymer concrete do not require Portland cement and hence, they can be considered as less energy intensive since portland cement is a highly energy intensive material. Apart from less energy intensiveness, the Geopolymer concretes utilize the industrial wastes for producing the binding system in concrete and thus can be considered as highly ecofriendly material. Reveals that Geopolymer strengths go up or increase with age of concrete. That compressive strength of Geopolymer concrete decrease with increase in fine aggregate content in the mix irrespective of curing period. That in terms of the relatively low cost of the by-product raw materials, Geopolymer concrete was expected to reduce the cost by 10-30% compared to the conventional concrete. Geopolymer concrete possesses all desirable mechanical and structural properties that make it an ideal choice for the construction Industry. The strength and durability properties of Geopolymer Concrete (GPC) have been reviewed and it can be concluded that the performance of Geopolymer concrete is excellent in terms of chemical and fire resistance as compared to ordinary Portland cement concrete. However, due to absence of standards more investigations on the behavior of Geopolymer concrete based on reactivity are required to know its effects. Found that fly-ash is the most widely used material for making geopolymer concrete and the optimum time of curing for fly-ash based geopolymer concrete is said to be 20 to 24 hours.
The reviews concluded that different sources (and even the same source, but different batch) of fly ash materials will give some different characteristics of the fly ash, where it would affect the synthesis process of the fly ash based geopolymer concretes. Concluded that the compressive strength of the geopolymer concrete is highly influenced by the amount of CaO content in the fly ash. Besides that, the compressive strength also increases as the amount of the hooked steel fibers increases
References
- Aradhana M (2018) Durability Characteristics of bio mass ash and slag based Geopolymer concrete. Int J Rec Sci Res. 9: 23786-23789.
[Crossref], [Google Scholar]
- Sharma SR, Poudyal AK, Devkota BM, Singh S (2014) Factors associated with place of delivery in rural Nepal. BMC Public Health 3: 306.
[Crossref], [Google Scholar]
- Leonard J, Ancelin O, Ludwig B, G Richard (2006). Analysis of the dynamics of soil infiltrability of agricultural soils from continuous rainfall-runoff measurements on small plots. J of Hydrol 326: 122-134.
[Crossref], [Google Scholar]
- Lal R (1991) Soil Structure and Sustainability. J of Sustain Agri 1: 67-92.
[Crossref], [Google Scholar]
- Seljeskog L, Sundby J, Chimang J (2006) Factors influencing Women's choice of place of delivery in rural Malawi: An explorative study. Afr J Reprod Health 10: 66-75.
[Crossref], [Google Scholar]
- Otieno JO (2015) Factors associated with home delivery in west Pokot county of Kenya. Adv Public Health 1-6.
[Crossref], [Google Scholar]
- Osae S, Asiedu DK, Banoeng-Yakubo B, Koeberl C, Dampare SB (2006) Provenance and tectonic setting of Late Proterozoic Buem sandstones of southeastern Ghana: Evidence from geochemistry and detrital modes. J Afr Ear Sci 44: 85-96.
[Crossref], [Google Scholar]
- Hayashi KI, Fujisawa H, Holland HD, Ohmoto H (1997) Geochemistry of approximately 1.9 sedimentary rocks from northeastern Labrador, Canada. Geochim Cosmochim Acta 61: 415-437.
[Crossref], [Google Scholar], [Indexed]
- Cullers RL, Podkovyrov VN (2002) The source and origin of terrigenous sedimentary rocks in the Mesoproterozoic Ui group, southeastern Russia. Precambrian Res 117: 157-183.
[Crossref], [Google Scholar]
- Floyd PA, Leveridge BE (1987) Tectonic environment of the Devonian Gramscatho basin, south cornwall: Framework mode and geochemical evidence from turbiditic sandstones. J Geol Soc 144: 531-542.
[Crossref], [Google Scholar]