Research Article, J Fashion Technol Textile Eng Vol: 10 Issue: 4
Analysis of Impact Factors on the Physical Properties of 100% Cotton 11 Plain Woven Fabrics
Shaharia Ahmed*
Department of Textiles, Zhongyuan University of Technology, Zhengzhou, Henan, China
Corresponding Author: Shaharia Ahmed
Department of Textiles, Zhongyuan University of Technology, Zhengzhou, Henan, China,
Tel: +234 806 4541 460;
E-mail: engr.shaharia@gmail.com
Received date: March 08, 2022, Manuscript No. JFTTE-22-58937;
Editor assigned date: 15 March, 2022, PreQC No. JFTTE-22-58937 (PQ);
Reviewed date: 31 March, 2022, QC No JFTTE-22-58937;
Revised date: 08 April, 2022, Manuscript No. JFTTE-22-58937 (R);
Published date: 11 April, 2022, DOI:10. 4172/ 2329-9568.1000247
Citation: Ahmed S. (2022) Analysis of Impact Factors on the Physical Properties of 100% Cotton 1⁄1 Plain Woven Fabrics. J Fashion Technol Textile Eng Res 10:4.
Abstract
The purpose of this article is to examine the physical characteristics of three different types of 100% cotton 1/1 plain woven fabrics. Fabrics like canvas, poplin, and voile are taken into consideration. These textiles have a 60-inch width in common. Tear strength, tensile strength, weight (g/m2 ), cover factor, shrinkage, air permeability, Martindale pilling resistance, and Ultra-Violet Transmission were all tested on the fabrics. The experiments were carried out using the ASTM & AATCC Standards test procedure, which is mentioned further down in this document. In comparison to poplin and voile, canvas cloth has superior weight and strength qualities. In comparison to the other two textiles, voile fabric had a higher value of shrinkage and Ultra-Violet Protection Factors (UPF). The air permeability of canvas fabrics is higher. The research is based on exercise, and the findings support textile specialists. Researchers will be able to pursue this field further because of our investigation.
Keywords: Construction, Strength, Air transmission, Cover factor, Ultra-Violet protector factor
Introduction
There is immense importance of this research in the field of cotton fabrics manufacturing industries as well as sellers. Different scholars worked regarding this investigation at different times where literature review exposed different consequences. Some of them were parallel and some of them were widely different. Woven fabrics are subjected to a wide range of complex deformations during usage [1]. Strength is directly related to the polyester content percentage of the cotton-polyester blended woven fabrics [2].
Woven fabrics are made by the interlacement of two different sets of yarns. In these two sets, one is called the warp and another is called the weft. Woven fabrics are made with the interlacement process of warp and weft at a right angle. Generally, woven fabrics are manufactured in weaving loom, and made of yarns woven on a warp and a weft [3]. Shrinking capacity is a very important factor for the clothing industry and very strict claims are made for this property. No more than 3% shrinkage in the cross and lengthways directions of the fabric is allowable. A matter of primary interest for fabric shrinking capacity is fabric structure, which is characterized by seven main parameters: Fabric warp and weft raw material, the linear density of warp and weft yarns, densities of warp, and weft, and fabric weave. All these factors together determine the fabric's formation, parameters, and characteristics [4].
Woven fabrics are mainly three types such as plain, twill, and satin. Plain weave fabrics are mainly manufactured by the two sets of yarns with the 1 up and 1 down process at right angles. The higher the surface openness, the lower or more negligible the influences of other factors on UPF values. The colour of a fabric plays an important role in UV ray protection in the samples with a sufficiently closed surface and especially black and blue colours exhibit high absorbance in the UV wavelength range and provide excellent protection when the samples are highly closed compact. Other chromatic colors, such as red, yellow and green also offer adequate very good protection against UV radiation [5]. In this weave, the warp and weft yarns stay at right angles and create a durable fabric. Every weft yarn passes the warp yarn by moving above one and then below the following, and so on. The subsequent weft yarn goes below the warp yarn that its belonging passes over, and vice versa [6].
In woven fabrics, there are mainly two cover factor values like warp cover factor and weft cover factor. Cover factor hangs on some issues like yarn count, thickness, density, and shape [7]. These yarns run parallel to their corresponding yarns. Muslin is a type of fabric that is made up of 100% cotton yarns with the interlacement portion of one up and one down. The yarn count of muslin clothes is very fine ranges from 200Ne to 300Ne [8]. With the higher interlacement ratio, plain weave fabrics showed the maximum cover factor values. Rigidity or compactness was less in the twill and satin weave compared to plain woven fabrics. More thread counts like EPI and PPI showed more cover factor values. Extra crimp from plain weave fabrics due to more interlacement ratio has a greater advantage for more weight (g/m2) values [9]. It can simply make a relationship between outward evenness and abrasion. Consequently, the higher the exterior zone of reproduction yarns, the greater would be the clothes balance and, hence, the higher would be the frictional confrontation [10]. This strength of woven cloth is one of the most significant characteristics which make it bigger in many applications as related to nonwoven and knitted clothes.
The property of shrinkage is expressed as the change of measurement through the length and width of the clothes after washing, either in hot water or in cold water . When cotton fabrics are submerged in water, they started to shrink in both warp and weft ways to neutralize pressures obtained from the processing finishing department. Shrinkage values are both types like positive and negative. Positive shrinkage refers that a fabric that will increase in length after washing. Wherein negative shrinkage fabrics started to shrink or reduce their length after washing [11]. The Cover factor is a technical dimension of the proportion area of the cloth enclosed by the yarns. The Cover factor is dependent on the construction of the clothes and the type of yarns used. Plain weave fabrics expressed the best cover factor values compared to twill and satin weave fabrics [12]. Air permeability is a property that measures how effortlessly air passes through the clothes. It specifies the breathability of fabrics. The more the air-permeability is, the better the breathability is. Air-permeable clothes have a habit to have moderately high moisture vapor diffusion capacities [13]. Canvas fabric expressed a higher value of weight and strength compared to poplin and voile, on the other hand, voile fabric expressed a better value of shrinkage compared to the other two fabrics [14] .
Materials and Methods
Materials used
100% cotton 1/1 plain woven fabrics were used in this research for the investigation of the physical properties of fabrics as stated in (Table 1). Three uncontaminated kinds of cotton of plain 1/1 weave fabrics with different construction and the same widths were used in this research. All the fabrics were of the plain weave in uncontaminated cotton yarns. Canvas fabrics are produced with 30Ne Warp and weft 30Ne weft yarn count with EPI 92 and PPI 78, poplin fabrics are produced with 38Ne warp and weft yarn count with construction EPI 102 and PPI 92. Voile fabrics are produced with 48Ne warp and weft count yarns belonging to construction EPI 110 and PPI 100.
Table 1: Materials used in this research.
Method Used
Specimens were performed following the test method provided by ASTM and AATCC Standard as mentioned underneath this paper. Allow the specimen to bring the equilibrium state in the standard atmosphere for test performance. Each specimen is directed in practice conditioning standard ASTM D1776.
The Experimentation
The experiment of weight (g/m2)
The weight of the specimen was taken in ASTM D3776 Standard. Weight was taken in mass per unit area of fabric. A round GSM cutter was used to take the weight of the samples. First, the fabrics were conditioned as per standard ASTM D1776 after taking from the industry. Fabrics were cut with the round GSM cutter at 5 different places to avoid selvage to get the average weight of the clothes. After cutting the fabric, it was placed in the measuring balance to get the results. The results were placed in table 2.
The experiment of tear strength
Tear strength was measured following the test method provided by ASTM D1424 standard using a pendulum apparatus. By the pendulum C in its original location, the two clamps were detached at a distance and associated in such a way that the clamped samples have stayed in a plane parallel to the axis. After cutting the samples at the middle using scissors, one part was clamped at the instrument and the other part was clamped at the pendulum in such a way that while splitting, the tear strength was recorded using the pendulum reading and positioned the results are obtained and put in table 2. Shows the tear strength measurement process of fabrics (Figure 1).
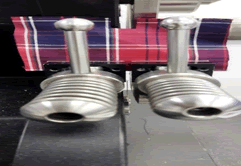
Figure 1: Tear strength measurement observed by James heal tear tester machine (Elmendorf).
The experiment of tensile strength
Following ASTM D5034 the tensile strength was measured, which is a grab test system for the measurement of breaking force and elongation of the woven fabrics. The fabric samples were cut in a size of 4-inch square shape. Then the samples were mounted with their clamp and a force was applied to break the specimen 12 inches/min extension with jaw separation 3 inches between two jaw schemes. The upper part and lower part of the samples were clamped at the jaw. Using a computer, a signal was given to start the machine until the fabric is destroyed of its 60% Ruptured due to upward force from the device where the downward clam is static [15]. In table 2, shows the tensile strength obtained process of fabrics (Figure 2).

Figure 2: By using titan 5 tensile strength measurement Observed.
Experiment of shrinkage
Dimensional stability or shrinkage of fabric was measured using AATCC 135 standard. The fabric was cut in 40-inch square size and interlock stitched was given at the edge of the clothes so that the yarns could not be removed from the fabric due to heavy laundry in a washing machine. The fabric was marked by a 36-inch square shape for measurement with a permanent marker. The sample was loaded on the machine and started washing at 60°C temperature for 5 minutes. Then the sample was rinsed wash at normal room temperature. After that, the sample was dried in the machine for 3 minutes with hot air blow. At last, the samples were pulled out and dimension was measured using measurement tape and the shrinkage values were detected and positioned in table 2.
Experiment of cover factor
The Cover factor specifies the extent to which the area of the cloth is covered by the yarns. It is the percentage of the area covered by the yarns to the total area of fabric. Cover factor also describes the compactness, solidity, and density of the fabric. Cover factor values of the samples were measured with equation 1 as stated below. Three types of samples from table 1 were taken and their cover factor was measured with this equation and placed the results in table 2. This equation needs the values of EPI, PPI, warp count, and weft count. Yarn count checked through ASTM D1059 standards.
Experiment of air permeability
Air permeability is the rate of airflow passing perpendicularly through a fabric between the two surfaces following the ASTM D737 standard. The rate of airflow is measured in ft3/min/ft2. Air permeability is the competence of a material to permit air to pass through the clothes. The assessment of air permeability is less where the clothes are stiffer. The air permeability principle was complex where fabrics were slackly woven. The air pressure kept for this test was 125Pa across the samples keeping the laboratory temperature 20°C with a relative humidity of 65% and the values were positioned in table 7 and (Figure 3).
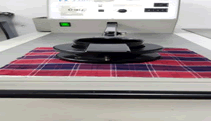
Figure 3: Air porousness transmission measurement process of fabrics.
Experiment of martindale pilling resistance
The Pilling resistance of the clothes was measured in contract with the test method provided by ASTM D4970 Standard. Specimen test conducted in the standard atmosphere. The fabric was cut 3 pairs of specimens where 3 pieces are 5.5 inches in diameter other 3 pieces 1.5 inches diameter. Mount one 5.5 inches diameter of standard felt and one fabric specimen of diameter. Placing one 1.5 inches diameter disk of 3 mm polyurethane foam and a specimen of the same 1.5 diameters of fabric in each holder. Start machine without any load run for 100 movements. The rating was taken individually and recorded as its average result.
Experiment of ultra-violet radiation protection resistance
Ultra-Violet Radiation (UV-R) is electromagnetic radiation, that we cannot see or feel, and its emitted by natural or artificial sources. The transmission of ultraviolet radiation (UV-R) through the fabric is measured on a spectrophotometer at known wavelength intervals. The Ultraviolet Protection Factor (UPF) is computed as the ratio of the erthemally weighted ultraviolet radiation irradiance at the detector with a specimen present. The Ultraviolet Radiation (UV-R) test is performed according to the AATCC-183 method. Test conducted in two conditions dry medium and wet medium. Specimens are cutting (50 x 50) mm square avoiding distorting and selvage areas (Figures 4 and 5). Test a minimum of two (2) specimens from each sample for the wet and the dry testing. Cut each specimen at least 50 × 50 mm (2.0 × 2.0 in.) or 50 mm (2.0 in.) in diameter. Avoid distorting the specimen during preparation and handling.
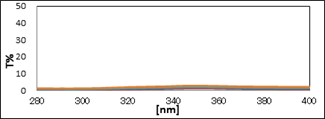
Figure 4: UV Protection Factor (dry condition) measurement.
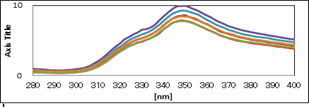
Figure 5: UV protection factor (wet condition) measurement.
Results and Discussion
Weight measurement
The specimen's weight in g/m2 was determined using the ASTM D3776 Standard's test technique. Table 2 displays the results. Table 2 shows that fabrics with a coarser yarn count have a heavier weight than those with a finer count. Canvas materials are always thicker than poplin and voile fabrics. An electric balance was used to determine the average weight of five specimens, which was then positioned in Table 2.
Analysis of tear and tensile strength
The specimen's slit strength was tested according to ASTM D 1424 Method. Using a falling pendulum equipment, this procedure generates a test report. Table 2 shows the strength values. It has been demonstrated that coarser fibers have more tear strength than finer fabrics. Because coarser yarns are stronger than finer yarns, this is the case.
The specimen's tensile strength was tested according to ASTM D 5034 Method. The breaking strength of fabrics is measured using this method. The central half of the sample is riveted in the jawline during this examination. Both the warp and weft directions were tested. Because it is sized with PVA weft yarn that is not sized, the warp direction extension percentage is minimal. The canvas cloth had the highest tensile strength, whereas the poplin and voile fabrics had lower tensile strength. The tensile and tear graphical representation is shown in (Figure 6).
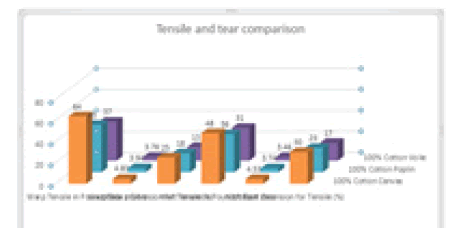
Figure 6: Graphical presentation of tear & tensile.
Shrinkage measurement
The fabrics' dimensional stability was determined using AATCC-135, which supplied the test procedure. This test method measures cotton fabric shrinkage in both the warp and weft directions. The EPI is higher than the PPI because the warp yarn was sized and the weft yarn was sized. The shrinkage report for various textiles is shown in Table 2.
Table 2: Physical properties of fabrics.
Measurement of cover factor
The area of woven fabrics covered by a single pair of strands is expressed as a cover factor. Based on the warp/weft ratio of the neighborhood's yarns, this value represents the tightness and looseness of materials. The cover factor of these fabrics is shown in Table 2. As can be seen from the chart, 100% cotton voile fabric has the highest cover factor value, while 100% cotton canvas fabric has the lowest cover factor value. Among these three samples, poplin fabric has the middle cover factor value.
Air transmission measurement
The ability of cloth to transmit air through it is known as air permeability. Where the materials are more rigid, the air permeability flow rate is lower. Where materials are loosely woven, air permeability ratings are higher. The ASTM D737 standard is used to verify air permeability values, which are then entered table 2. The air permeability measurements were measured in feet per minute (ft3/min). The table shows that 100% cotton canvas has the highest air permeability value (Figure 7). The air permeability value of 100 percent Cotton Voile, on the other hand, was the lowest. It was discovered that the fabric's architecture and yarn count are directly responsible for air transmission through the fabric surface.
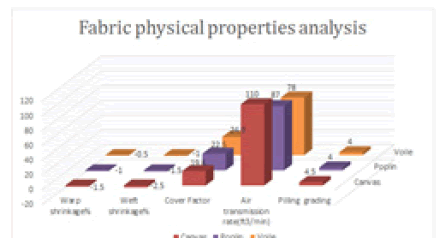
Figure 7: Graphical presentation of shrinkage, cover factor, air transmission, pilling resistance.
Grading of martindale pilling resistance
This method covers the determination of the resistance to the formation of pills and other related surface changes on fabrics using the Martindale tester. Followed by ASTM D4970 standard, pilling grades are verified and placed in (Table 2). The experimental resistance to pilling is reported on an arbitrary scale ranging from 5 to 1 (No pilling to severe pilling). It is understood from the table that 100% cotton canvas exposed the maximum pill resistance value. Alternately, 100% Cotton Voile exposed the lowest pill resistance against face to face rubbed.
Measurement of ultra-violet protection factor
To measure the degree of UVR protection of fabrics, the Ultraviolet Protection Factor (UPF) is defined as the ratio of average effective UV radiation irradiance transmitted and calculated through the air effective dose–ED to the average effective UV radiation irradiance transmitted and calculated through the fabric (effective dose-EDf) (EN 13758-1, 2002; Scott, 2005) UV light flows through the open areas of fabrics macropores and through the yarns, where it changes direction before leaving the fabric with scattered UV transmission. Numerous researches have been conducted on several fabric constructional characteristics that best describe the fabric structure and have a direct and significant impact on UV protection. Fabric cover factor, fabric open porosity, fabric mass, fabric thickness, and other factors have all played a part. The UVR spectrum can be subdivided into near UV (400-300 nm), middle UV (300–200 nm), and vacuum UV regions (200–10 nm) by physicists, or into UVA (400–315 nm), UVB (315–280), UVC (280–100 nm) and UVD (100-10 nm) regions by biologists.
Conclusion
The physical features of 100% cotton 1/1 plain woven fabrics were detailed throughout the research, and new research focusing on the topic was reviewed in this publication. These textiles had a 1/1 plain weave structure and came in a variety of forms, including canvas, poplin, and voile. In comparison to poplin and voile fabrics, canvas fabrics have a thicker form and thickness. In comparison to the other two textiles, poplin and voile, it has the highest tear, tensile strength, and pilling resistance. Due to tight, loose strands and interwoven warp yarns in the weft, canvas textiles shrink -2.5% less than poplin and voile fabrics. Despite its bulkier appearance, it had a cover factor of 25.6.
The appropriate combination of the characteristics allows for the manufacture of UV-protective passive woven fabrics, which may lower the danger of UV overexposure. The number of EPI and PPI with a yarn count and type of weave, yarn fineness, fabric tightness, fabric cover factor, and Ultraviolet Protective Factor (UPF) with GSM values is proven to directly stimulate the physical qualities of the fabric, except for shrinkage values seen reversed. The findings of this study are relevant to those working in the textile industry that is responsible for producing cotton-woven fabrics and managing their physical qualities as intended end products.
Conflicts of Interest
The author reports no conflicts of interest. The authors alone are responsible for the content and writing of this article.
Acknowledgement
The author is thankful to the physical testing department of SGS Bangladesh Ltd (Dhaka, Bangladesh) for their continued care regarding test manipulation.
The author also indebted Professor Shan Du, College of Textiles, Zhongyuan University of Technology, Zhengzhou, Henan, China.
References
- Hu J, Xin B (2008) Structure and mechanics of woven fabrics. Wood head Publ ser Tex 48-83.
[Crossref], [Google Scholar]
- Islam S, Ahmed S, Arifuzzaman AKMS, Arifuzzaman Md, Shilpi A (2019) Relationship in between strength and polyester content percentage of cotton polyester blended woven fabrics. Int J Clothing Sci 6: 1–6.
[Crossref], [Google Scholar]
- Hussain A, Podgursky V, Goljandin D, Viljus M, Antonov M, et al. (2021) Tribological and mechanical properties investigations of post-consumer cotton textiles. In Solid State Phenomena 320: 97-102.
[Crossref], [Google Scholar]
- Milašius V, Milašius A, Milašius R (2001) Comparison of integrating structure factors of woven fabric. Materials Science (Medžiagotyra) 7: 48-53.
[Crossref], [Google Scholar]
- Gabrijelcic H, Urbas R, Sluga F, Dimitrovski K (2009) "Influence of fabric constructional parameters and thread colour on UV radiation protectionË®. Fibres Text East Eur 17: 46-54.
[Crossref], [Google Scholar]
- Muzaffar S, Abbas M, Siddiqua UH, Arshad M, Tufail A (2021) Enhanced mechanical, UV protection, and antimicrobial properties of cotton fabric employing nano chitosan and polyurethane-based finishing. Journal of Materials Research and Technology. 11: 946-956.
[Crossref], [Google Scholar]
- Iftikhar F, Ali Z, Hussain T, Nazir A, Adolphe DC (2021) "Influence of yarn count and cover factor on mechanical, comfort, aesthetic and hand properties of ladies' summer apparel fabricsË®. J Nat Fiber 18: 1592-1603.
[Crossref], [Google Scholar]
- Abd El-Hady MM, Sharaf S, Farouk A (2020) Highly hydrophobic and UV protective properties of cotton fabric using layer by layer self-assembly technique. Cellulose 27: 1099-1110.
[Crossref], [Google Scholar]
- Islam S, Akter S, Ahmed S (2022) influence of cover factor on the physical properties of woven fabrics. J text polym 10: 57-63.
[Crossref], [Google Scholar]
- Jadhav P, Dhole P, Turukmane R (2018) "Investigation an impact of weft count and pick densities on allied fabric propertiesË®. Int J Text Eng Proc 4: 14-17.
- Baruah S, Kalita BB, Jose S, Borah MP (2021) "Impact of weave on physico-comfort properties of eri/modal union fabricË®. J Nat Fiber 1-9.
[Crossref], [Google Scholar]
- Wei Y, Gong RH, Ning L, Ding X (2018) Research on physical properties change and damage behavior of cotton fabrics dried in drum-dryer. J Text Inst 109: 121-132.
[Crossref], [Google Scholar]
- Hunter L, Fan J (2015) "Adding functionality to garmentsË®, In: Textiles and Fashion, Materials, Design and Technology, Woodhead Publishing Series in Textiles. Elsevier 705-737.
- Ahmed S. (2021) A study on the physical properties of 100% cellulosic woven fabrics. J fash technol text eng 7(4): 127â??132.
[Crossref], [Google Scholar]
- Transmittance. (2020) Blocking of Erythemally weighted ultraviolet radiation through fabrics. AATCC Test Method 183.
[Crossref], [Google Scholar]