Research Article, J Fashion Technol Textile Vol: 11 Issue: 1
Fusion of Design and Technology in Creating Color-Changing Smart Home Textiles: A Practice-Based Approach
Joe AU, Jin LAM* and Gloria WU
School of Fashion and Textiles, The Hong Kong Polytechnic University, Hunghom, Kowloon Hong Kong
*Corresponding Author: Jin LAM
School of Fashion and Textiles,
The Hong Kong Polytechnic University,
Hunghom,
Kowloon,
Hong Kong
E-mail: jin.lam@polyu.edu.hk
Received: 24-Dec-2022, Manuscript No. JFTTE-22-84542; Editor assigned: 27-Dec-2022, PreQC No. JFTTE-22-84542(PQ); Reviewed: 13-Jan-2023, QC No. JFTTE-22-84542; Revised: 20-Jan-2023, Manuscript No. JFTTE-22-84542(R); Published: 27-Jan-2023 DOI: 10. 4172/2329-9568.1000279.
Citation: Joe AU, Jin LAM, Gloria WU (2023) Fusion of Design and Technology in Creating Color-Changing Smart Home Textiles: A Practice-Based Approach. J Fashion Technol Textile 11:1.
Abstract
This paper describes a practice-based approach to creating an interactive, color-changing, smart dining tablecloth controlled via a mobile app by the user for the modern interior. By integrating intelligent weaving structures, materials, optic fibers and a radar sensor, the author applies a theoretical design process model to develop a smart textile product tailored toward general consumers’ intuitive operation. The colorchanging smart home textile prototype produced can be applied in other textiles products to satisfy consumers with diverse lifestyles and preferences. Both textile industry and textile design practitioners including textile design students can benefit from this study’s theoretical and practical contributions.
Keywords: Color-changing; Smart home textiles; Design process model
Introduction
This study combined the theories of color-changing and weaving technologies along with practical concept development to create a high-end interior home textile design. As advanced technology is fueling the development of smart textiles and e-textile solutions for indoor environments the smart textiles are considered important for the future home [1]. The creative design and application of colorchanging textiles can provide lots of possibilities for smart products. This will not only add values to consumers’ lives, but will also satisfy the demand for market development in the textile industry [2]. As optical fibers could be embedded in textiles as embroidery and in weaving process, the color-changing feature in textile design has become popular in the recent years. After reviewing the latest illuminative and color-changing interior products in the market and their application in aesthetically pleasing designs, we identified the technologies of illumination, sensor application, and specific circuit designs suitable for interior textiles as those that promise an attractive user experience and could be integrated into home textile products. We devised a smart tablecloth prototype for indoor use. The specific objectives of this study were as follows:
• To develop a theoretical design process model for color-changing smart home textiles,
• To finalize a detail design specification for color-changing smart home textiles, and
• To create a high-end, color-changing smart home textile prototype-a “smart dining tablecloth”-that could be a success in the current interior and home textiles market.
We hope that this study will increase awareness of the aesthetic and functional aspects of color-changing smart home textiles and promote more novel designs in the modern textile industry. The proposed design process model of color-changing smart home textiles illustrates innovative design and development principles for contemporary interior home textile products that can meet ever-changing consumer requirements. This study provides theoretical and practical contributions that are crucial to textile industry and textile design practitioners including designers and students.
Methodology
A practice-based research methodology was adopted in this study. Art and technology expert Linda Candy characterized practice-based research as “an original investigation undertaken in order to gain new knowledge partly by means of practice and the outcomes of that practice” [3]. The definition of practice-based research is similar to that of any research not exclusively concerned with theoretical analysis. The research process is complete when understandings reached are considered transferrable. Original contributions to knowledge may include artifacts such as images, music, designs, models, digital elements, media, performances and exhibitions with creative outcomes. The advantage of using a practice-based research method is, “the articulation of design processes in such a way as to bring clarity to the skills, orientation and processes that shape the development of design outcomes” [4].
Development of a theoretical design process model of colorchanging smart home textiles
We developed this theoretical design process model of colorchanging smart home textiles based on French’s design process model as well as a product development process and an engineering approach to industrial design (Figure 1) [5]. A main feature in French’s model is the possibility of going round the design cycle. At almost every stage, the designer is expected to re-examine earlier stages to make amendments until a satisfactory solution is found. The main processes are as follows: (a) identification of needs, (b) analysis of problems, (c) conceptual design, (d) development of initial prototypes, (e) evaluation, (f) solution and (g) detail design.
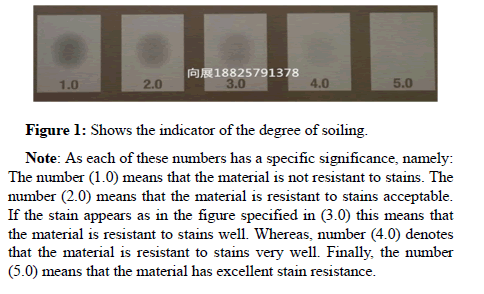
Figure 1: Theoretical design process model for color-changing smart home textiles.
Identification of needs: The information necessary to begin a design is usually based on detailed marketing studies that determine a requirement for a new product or service. In one of the successful processes used, users’ needs and the context of use must be understood [6]. A review of current smart home textile products on the market and of the related materials and techniques applied in smart fashion and textile designs-such as various illuminative and colorchanging materials, sensors, weaving techniques and processesindicates that consumer demand exists for interactive smart home textiles in the current market setting. The development of smart textiles with self-functioning capabilities has been speed up increasingly with new technologies and the color-changing textiles are identified as a way to add features into common textiles. Schwartz, et al. indicated that “further developments using smart material may offer added value because these materials have the ability to control light, temperature and color” [7].
Analysis of problems: Some design process models emphasize the need for extensive analytical work to be undertaken before conceptual solutions are developed. Such analysis involves investigating relationships, searching for patterns in the information available and categorizing objectives. In this study, the main objective is to create a color-changing smart dining tablecloth that can be a success in the current interior and home textiles market. A review of recent smart textiles in the market including, smart carpet, tapestry for home decoration and user-controlled curtains showed that the sub-problems involve the selection of color-changing materials, sensors, yarns and weaving technologies. Analysis of the problem is a small but important part of the overall design process [8-10].
Conceptual design: Conceptual design refers to the process of generating design alternatives. This project aims to design a smart dining tablecloth controlled via a mobile app by the user for the modern interior. The user can trigger the LED lights to illuminate the optical fiber of the tablecloth by pressing any of the mode control buttons including the speed, choice of colors and lighting pattern within the mobile app. The project necessitated the development of four conceptual design elements: (a) color-changing materials; (b) various sensors; (c) suitable yarns and (d) weaving technologies. In the overall design process, conceptual design places the greatest demands on designers, whose main task is to identify areas of improvement.
Development of initial prototypes: In this prototype development stage, designers refer to feedback from the conceptual design stage. The prototypes are further refined and then a final choice is made between experimental models. A rectangular tablecloth was woven with a handloom machine by using 100% cotton yarn, 100% polyester yarn, flame retardant polyester yarn and 500 mm of pretreated optical fiber. The prototypes were divided into four main groups, each of which had different yarn type compositions but the same basic weaving structures-plain weave, basket weave and check weave-to determine the optimal design. The prototypes were woven with the handloom machine because the pretreated optical fibers were not suitable for weaving using a Jacquard loom machine; such an approach may have damaged the machine or the pretreated optical fibers. This was also the main reason why these prototypes were not woven using complicated weaving structures. The 12 initial smart dining tablecloth prototypes are illustrated in Figure 2. Initial prototypes of smart dining tablecloth.
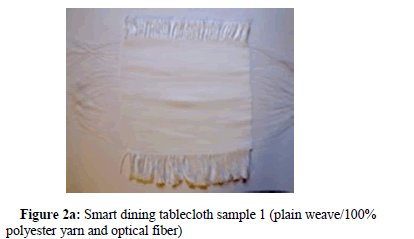
Figure 2a: Smart dining tablecloth sample 1 (plain weave/100% polyester yarn and optical fiber).
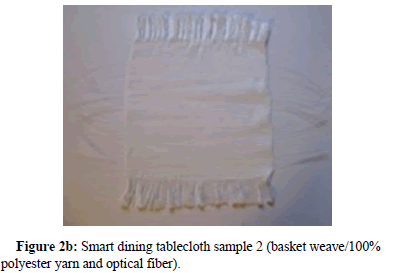
Figure 2b: Smart dining tablecloth sample 2 (basket weave/100% polyester yarn and optical fiber).
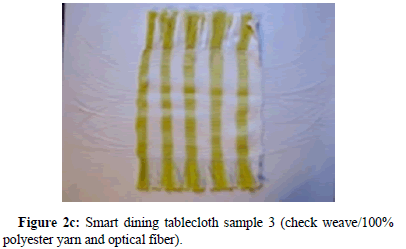
Figure 2c: Smart dining tablecloth sample 3 (check weave/100% polyester yarn and optical fiber).
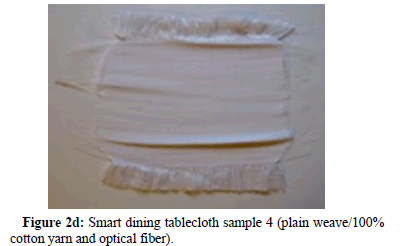
Figure 2d: Smart dining tablecloth sample 4 (plain weave/100% cotton yarn and optical fiber).
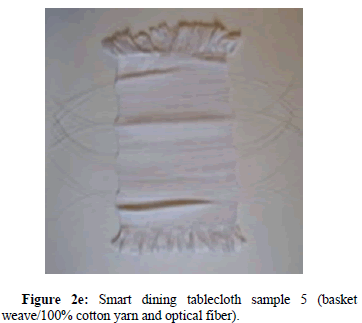
Figure 2e: Smart dining tablecloth sample 5 (basket weave/100% cotton yarn and optical fiber).
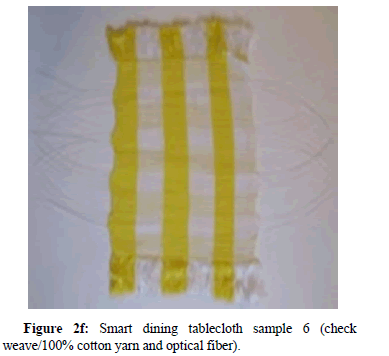
Figure 2f: Smart dining tablecloth sample 6 (check weave/100% cotton yarn and optical fiber).
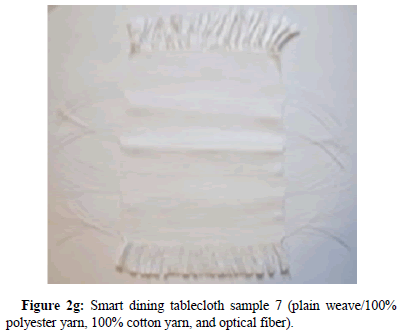
Figure 2g: Smart dining tablecloth sample 7 (plain weave/100% polyester yarn, 100% cotton yarn, and optical fiber).
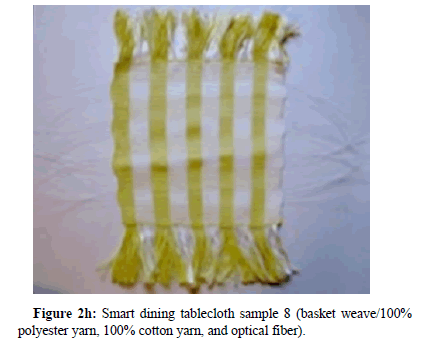
Figure 2h: Smart dining tablecloth sample 8 (basket weave/100% polyester yarn, 100% cotton yarn, and optical fiber).
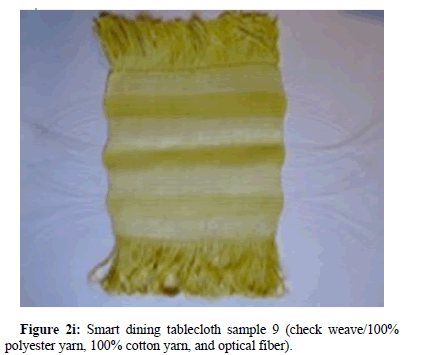
Figure 2i: Smart dining tablecloth sample 9 (check weave/100% polyester yarn, 100% cotton yarn, and optical fiber).
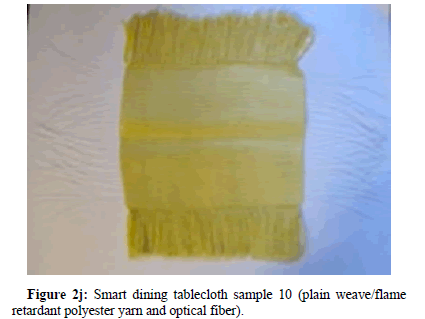
Figure 2j: Smart dining tablecloth sample 10 (plain weave/flame retardant polyester yarn and optical fiber).
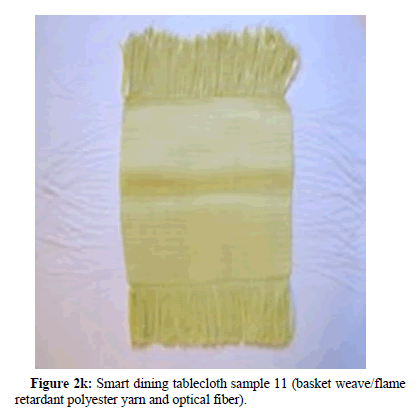
Figure 2k: Smart dining tablecloth sample 11 (basket weave/flame retardant polyester yarn and optical fiber).
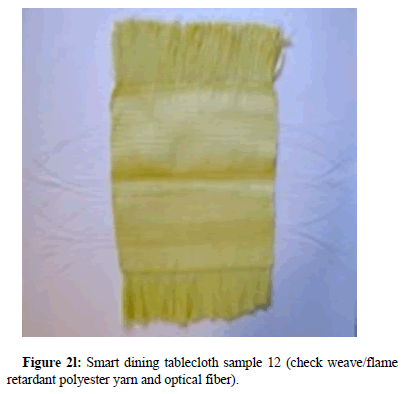
Figure 2l: Smart dining tablecloth sample 12 (check weave/flame retardant polyester yarn and optical fiber).
Light-Emitting Diode (LED) light sources and radar sensors were integrated with the handwoven fabrics. The radar sensors were able to detect people approaching within a distance of 1 feet from the sensor. Once the radar detected an object within this space, the LED light source’s power was switched on and the optical fibers lit up. Hence, if a person wished to retrieve something from the dining table late at night, they would not need to turn on the light for illumination. Figure 3 depicts the test scenarios of the color-changing and illuminative effects of the optical fibers transmitting light from the LED light source. Figure 3a illustrates the LED light source configuration for supplying power and light to the optical fibers. Once the LED light source was switched on, the common colors, namely white, green, red and blue, could be selected (Figure 3b-3e). Test scenarios showing the color-changing effects of optical fibers.
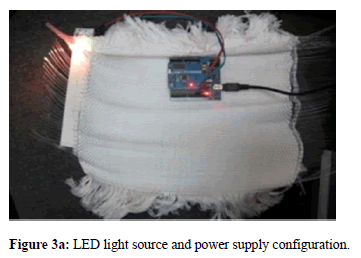
Figure 3a: LED light source and power supply configuration.
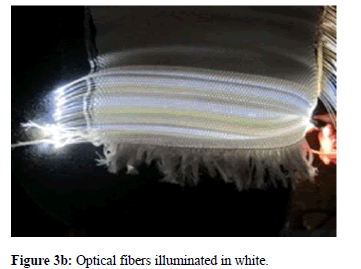
Figure 3b: Optical fibers illuminated in white.
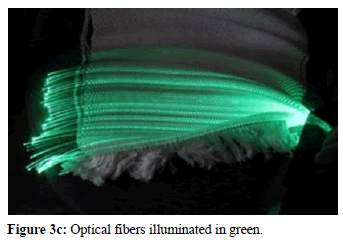
Figure 3c: Optical fibers illuminated in green.
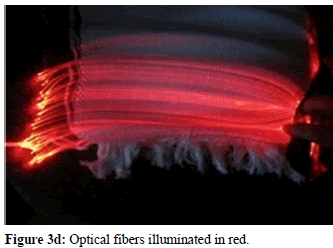
Figure 3d: Optical fibers illuminated in red.
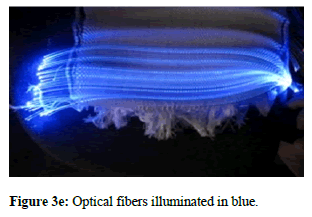
Figure 3e: Optical fibers illuminated in blue.
Results
Evaluation
The initial prototypes were evaluated according to the technological characteristics of the color-changing materials, sensors and weaving structures that could be integrated into the smart home textiles. Product concept evaluation is a critical step in concept development. The aim of an evaluation is to arrive at a decision on whether to discontinue, reiterate, or commence full usage of the concept.
Abrasion test: Because the smart tablecloth was woven with pretreated optical fibers, it was not suitable for testing using an abrasion testing machine. Also, according to the American Society of Testing and Materials’ D4966 abrasion test method, the fabric was not suitable for testing because a testing specimen must have a diameter smaller than 38 mm; a fabric that is overly thick would break the test machine’s razor blades [11].
Lux test: The lux test results revealed that both white and blue illumination had the same highest lux test results of 4, as determined using a digital lux meter, and the associated prototypes had the same yarn compositions of 100% polyester, 100% cotton, and optical fibers with basket weave structures. The basket weave structure had a chessboard appearance similar to that of a plain weave structure. The durability of the basket weave fabric was better than that of the plain weave fabric because it had a higher abrasion resistance rate. Therefore, we concluded that these white and blue basket-woven structures were optimal choices for the final smart dining tablecloth design.
Solution
After the evaluation process, some individual solutions were created based on technological and functional requirements. This solution building represents the most important task of a designer within the design process. Designers should adapt their own processes to respond to various problem structures. Textile designers should produce sample fabrics based on certain design solutions and a series of samples, each representing a certain variation in the particular design solution. Then, the relevant fabrics can be selected from these samples. Moreover, weaving performance and dimensional stability are essential criteria in a design process firmly grounded in best practice within industry settings [12].
Detail design
Detail design is the final stage of the design process and involves final prototype development. In this stage, all drawings and other production-related documents were finalized. Details of our prototype covered the following items: (a) coloration, (b) color-changing material, (c) yarn type, (d) weaving structure, (e) graphic pattern and (f) sensor. Finally, an interactive color-changing smart home textile prototype was created.
Coloration: White and yellow were the main visible colors in the smart dining tablecloth when it was switched off. However, one of several colors, namely white, blue, green and red, could be visible when the LED light source was activated. Thus, our prototype design solution allowed for multiple user selections. Consumers could activate any of the four colors by using an associated mobile app. White and yellow were the main colors for the ‘Smart Dining Table Cloth’ when it was switched off. However, when it was turned on, it changed to multi-colors as it was connected with the LED lights with colors in white, blue, green and red. All visible colors are light energy and derive from the electromagnetic spectrum, whose wavelengths determine colors [13]. The specific visual color is created after colors themselves are recognized in our visual brain [14,15]. This was the prototype using different colors to present the design idea. Consumer could pick any color they like by using the remote.
Color-changing materials: The color-changing materials in our design were the LED lights and optical fibers. The pretreated optical fibers were woven into the fabric using a handloom machine. The optical fibers emitted visible light when LED light was projected through them.
Yarn type: The yarn type was a combination of 100% cotton, 100% polyester, flame retardant polyester yarn and optical fiber. These yarns were combined using a basket weave structure, which produced the best woven fabric durability. The mixture of 100% cotton and 100% polyester yarn produced the most durable fabric, and the flame retardant polyester yarn helped prevent overheating or fire risks from extended contact with the LED light source while retaining the desired abrasive properties.
Weaving structure: Basket weave was the principal weaving structure used in the smart tablecloth’s production. The advantages of the basket weave structure were that it promoted the effect of optimal illumination from the optical fibers and was the most durable among the weaving structures tested.
Graphic pattern: This smart dining tablecloth had no specific graphic design of pattern because it was woven by a handloom machine and the internal optical fibers were too fragile to be bent. Hence, it was not suitable to use the Jacquard loom machine to produce complicated woven structures within the fabric. A basket weave was used to highlight the multiple colors of the dining tablecloth when it was illuminated by the LED light source.
Sensor: A radar detection sensor was embedded into the smart dining tablecloth. When the radar sensed an object moving within a 1- foot radius, it sent a signal to the main circuit board to activate the LED lights and illuminate the optical fibers. Alternatively, the sensor could be deactivated using the associated mobile app. The user could trigger the LED lights by pressing any of the mode control buttons within the mobile app. Figure 4 illustrates the steps required to connect the smart dining tablecloth.
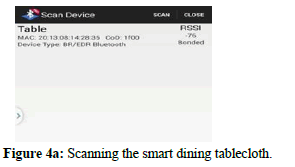
Figure 4a: Scanning the smart dining tablecloth.
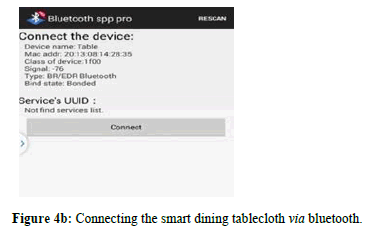
Figure 4b: Connecting the smart dining tablecloth via bluetooth.
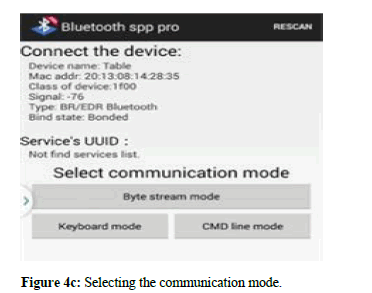
Figure 4c: Selecting the communication mode.
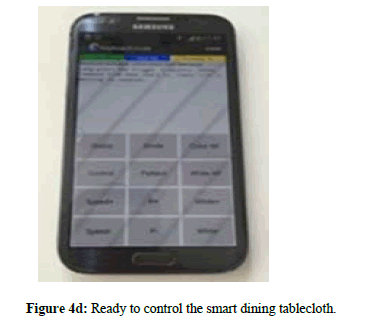
Figure 4d: Ready to control the smart dining tablecloth.
Presentation of the color-changing smart dining tablecloth
Figure 5 shows the electronic components, which consisted of power supply (Figure 5a) providing electricity for the LED light source (Figure 5b) embedded in the smart dining tablecloth. The power supply was connected to the motherboard (Figure 5c) and radar (Figure 5d). The complete configuration of the electronic components is shown in Figure 5e. Electronic componentry embedded in the smart dining tablecloth.
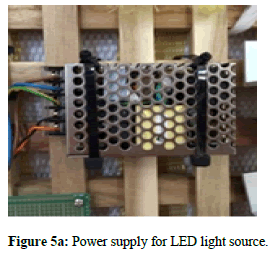
Figure 5a: Power supply for LED light source.
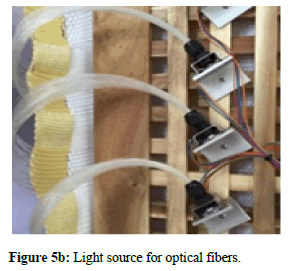
Figure 5b: Light source for optical fibers.
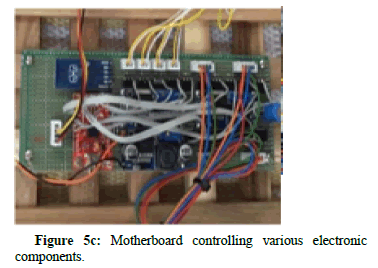
Figure 5c: Motherboard controlling various electronic components.
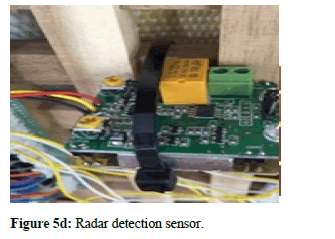
Figure 5d: Radar detection sensor.
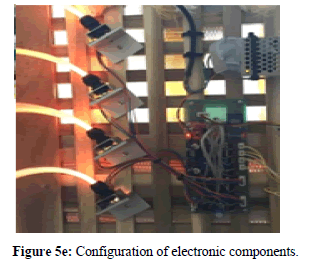
Figure 5e: Configuration of electronic components.
Once activated, the LED lights transmitted light along the optical fibers and created a color changing, illuminative effect. The final prototype of the smart dining tablecloth is depicted in Figure 6. Smart dining tablecloth.
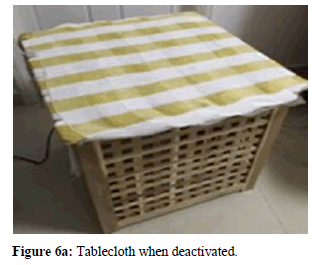
Figure 6a: Tablecloth when deactivated.
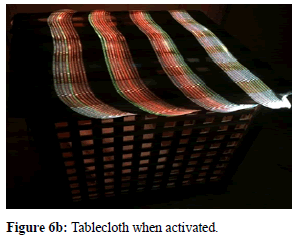
Figure 6b: Tablecloth when activated.
Discussion and Conclusion
This practice-based study combined weaving technology, practical concept development and the prototyping of color-changing smart home textiles. Our final prototype has promising theoretical and practical implications for textile design. Both fashion and textile design education can also benefit from expanded knowledge on colorchanging smart home textiles from aesthetic and functional perspectives. Furthermore, the prototypes we developed can be applied in diverse textile products and promote novelty in the textile industry.
The design process model we developed will interest designers and design students involved in creating new smart home textile prototypes. Understanding each step would assist designers and students in ascertaining the best solution for their design problems throughout the design process. We created the final smart home textile prototypes according to a theoretical design process model in this practice-based study, and our study extends previous scholarship through the unique approach taken in textile design. The smart dining tablecloth technology can be applied for commercial purposes, such as stage decoration, advertisement, and health and safety.
In conclusion, home textiles play a crucial role in the interior environment of a home by affecting the home interior not governed by architecture, such as texture, color, character and scale. Further research into smart fabrics is required to enhance the textile field and stimulate the creation of additional smart products for the fashion and textile markets.
References
- Mills Senn P (2020) Smart textile and e-textile solutions for indoor environments.
- Ramlow H, Andrade KL, Immich AP (2021) Smart textiles: An overview of recent progress on chromic textiles. J Text Inst 112(1):152-171.
- Candy L (2006) Practice based research: A guide. CCS report. 1(2):1-9.
- McLaughlin SM (2006) Valuing insight and judgement: A hermeneutic perspective on the development of validating contexts for practice-based research in design. Speculation and Innovation: Applying practice led research in the creative industries.
- French MJ, Gravdahl JT, French MJ (1985) Conceptual design for engineers. London: Design Council
- Takala R, Keinonen T, Mantere J (2006) Processes of product concepting. InProduct concept design 57-90.
- Schwarz A, van Langenhove L, Guermonprez P, Deguillemont D (2010) A roadmap on smart textiles. Text Prog 42(2): 163
- van Keymeulen B, Claeren P, van den Storme G, Andries D, Bossuyt F, et al. (2015) Smart carpet. Smart Textiles Salon 4, Ghent: 4-50.
- Ligorano N, Reese M (2021) Certainty and Ambiguity. Ligoranoreese
- Abrasion Resistance by the Martindale Method (2004) Standard test method for abrasion resistance of textile fabrics.
[Crossref]
- BaĆ?er G (2008) Engineering approach to industrial design of woven fabrics. Int J Fash Des. 1(2):79-87.
- Koenig B (2012) Color workbook (4th edtn). Upper Saddle River: Pearson
- Zeki S, Cheadle S, Pepper J, Mylonas D (2017) The constancy of colored after-images. Front Hum Neurosci. 11:229.
[Crossref] [Google Scholar][PubMed]
- Das S (2010) Fibres and fabrics used in home textiles. Perform Home Text.22-41.
- Cherenack K, van Pieterson L (2012) Smart textiles: Challenges and opportunities. J Appl Phys. 112(9):091-301.